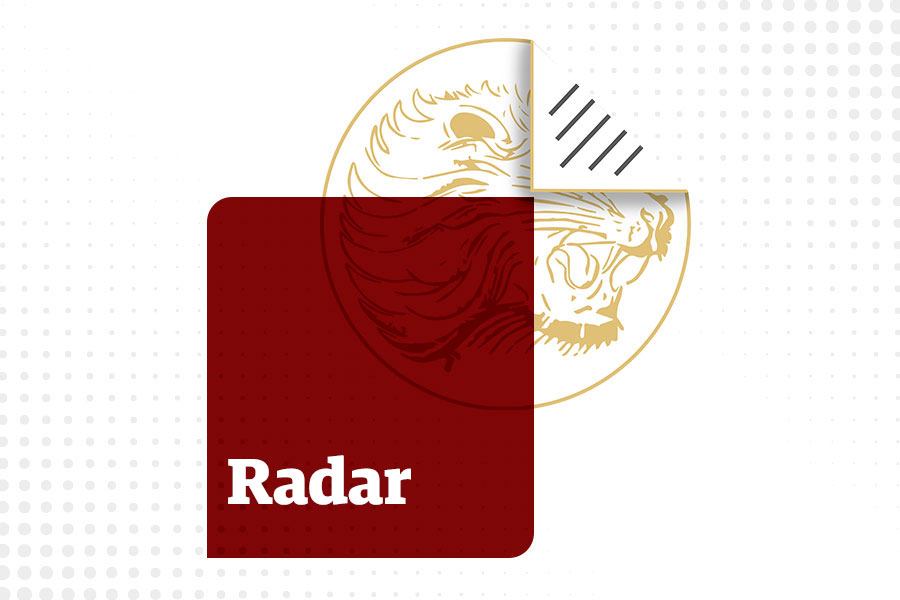
Radar | Jan 11,2020
Mar 13 , 2021
By Zelalem Bezabih
Cement has become a rare commodity. Ironically, as more developed countries suffer from a lack of demand in the market, we are struggling to fill a supply gap. Retail stores across Addis Abeba are short of construction material. Common cement retail market areas in Megenagna, Gojam Berenda, Gotera and Saris are like ghost towns these days.
With more than 21 cement manufacturing plants in Ethiopia, the past three years of aggravated chronic shortage is intolerable. The six major producers – Dangote, Derba, Messobo, Mugher, National and Habesha – produce nearly the entire supply. The projected actual market demand for cement is over 10 million tonnes. With almost 16.5 million tonnes of cement in annual production capacity and 10pc average year-on-year growth in consumption, Ethiopia is regarded as among the top cement producers in Sub-Saharan Africa, according to World Highways.
There is no construction without cement. But the construction industry, one of the fastest-growing over the past two decades, contributes 16pc to Ethiopia’s gross domestic product (GDP).
How come we are unable to resolve the underlying issues leading up to the current drastic shortage in the market?
The factory prices of each of the major cement producers have not shown as significant an escalation as retail prices. On average, factory gate prices for any one of the major producers is 365 Br a quintal. Whereas, the retail price in Addis Abeba is more than 600 Birr on average.
Manufacturers are often heard complaining that this is because the government does not listen to their ideas and appeals. Failure to establish close and functional relations between cement manufacturers and users is a significant obstacle, they insist. Instead, government directives are enacted based on unstructured and poor guidelines, which in turn restrict production.
Cement shortage has been blamed on lack of spare parts, power outages, lack of inputs, lack of leadership and professional skills, security problems, and the supply of raw materials at one time or another. Only 14 of the factories are active now, but many active ones are producing under capacity as well.
We have known about this for a long time, but what have we done to solve the issue?
The multiplier effect of construction interruption has a crippling effect on the overall economy of the country. On top of the direct employment impacts, there are companies that use cement as raw materials, such as household consumers, iron and metal manufacturers, PVC and roofing producers, and construction chemical manufacturers. The danger of falling short in achieving the target is vivid, and the loss in income has a transcending impact on the livelihood of millions as we speak.
There are some efforts to address the issue, though how successful they will be is questionable. The recently launched Lemi National Cement Industrial Complex project can only be regarded as a long-term solution, as it could take several years to finish. The 2.2-billion-dollar megaproject could have a game-changing role but cannot be seen as a remedy for the current mess.
With production capacity at 2.5 million tonnes a year, Abay Cement is much closer to commencing production, but it seems that there is no reason that uncertainties facing the currently operational manufacturers would not be expected to neglect Abay as well.
The Minister of Trade & Industry is probably as confused as consumers in resolving the chronic cement shortage. They seem to be of the view that, at the moment, the best the government can do is prioritise which projects get access. This is understandable.
But is this sustainable? Should the rest of the economy be neglected?
There should be mechanisms whereby the private sector can get cement with ease. Be it availing adequate forex for import or rotating local access, such a hollow response to one of the largest employing sectors in the economy is inconsiderate.
Clearly, past efforts to increase cement availability in the market failed miserably. Efforts like prioritising forex supply for raw material imports and improving steady electricity supply are either not enough or not implemented properly.
The chaotic cement market is not a result of an abrupt incident. This has been a long time coming. Industry insiders blame the government’s ineffectiveness for ensuring that production is streamlined and uninterrupted. In contrast, the government blames producers for failing to catch up with evolving developments and accuses retailers of hoarding.
Although cement import was recently allowed for the first time since 2013, expensive logistics prices have made it unrealistic to supply to the local market. This is neither attractive nor feasible to import by private traders. The better alternative is to offer affordable logistics prices or follow a wheat import-like procedure of direct buying until we get all the local manufacturers back to production.
The prospect of the cement market returning to normalcy is bleak, at least for the near future. Industry experts claim market stability is not expected until the end of the year unless urgent remedies are taken.
The question remains, can we afford to lose more jobs and more economic gains for the foreseeable future?
PUBLISHED ON
Mar 13,2021 [ VOL
21 , NO
1089]
Radar | Jan 11,2020
Radar | Jul 11,2021
View From Arada | Mar 25,2023
Radar | Jan 26,2019
Radar | Jun 12,2023
My Opinion | 132372 Views | Aug 14,2021
My Opinion | 128797 Views | Aug 21,2021
My Opinion | 126700 Views | Sep 10,2021
My Opinion | 124306 Views | Aug 07,2021
Dec 22 , 2024 . By TIZITA SHEWAFERAW
Charged with transforming colossal state-owned enterprises into modern and competitiv...
Aug 18 , 2024 . By AKSAH ITALO
Although predictable Yonas Zerihun's job in the ride-hailing service is not immune to...
Jul 28 , 2024 . By TIZITA SHEWAFERAW
Unhabitual, perhaps too many, Samuel Gebreyohannes, 38, used to occasionally enjoy a couple of beers at breakfast. However, he recently swit...
Jul 13 , 2024 . By AKSAH ITALO
Investors who rely on tractors, trucks, and field vehicles for commuting, transporting commodities, and f...
Jul 19 , 2025
Parliament is no stranger to frantic bursts of productivity. Even so, the vote last w...
Jul 12 , 2025
Political leaders and their policy advisors often promise great leaps forward, yet th...
Jul 5 , 2025
Six years ago, Ethiopia was the darling of international liberal commentators. A year...
Jun 28 , 2025
Meseret Damtie, the assertive auditor general, has never been shy about naming names...
Jul 19 , 2025 . By AMANUEL BEKELE
Federal lawmakers have finally passed the long-anticipated startup law, setting the s...
Jul 19 , 2025 . By BEZAWIT HULUAGER
An aggressive push by federal authorities to digitise fuel sales has ignited a market...
Jul 19 , 2025 . By NAHOM AYELE
A new lawsuit filed by Hailu Shawel's, once a towering figure in both engineering and...
Jul 19 , 2025 . By YITBAREK GETACHEW
The Federal Supreme Court has unveiled a sweeping plan to digitise the judicial syste...