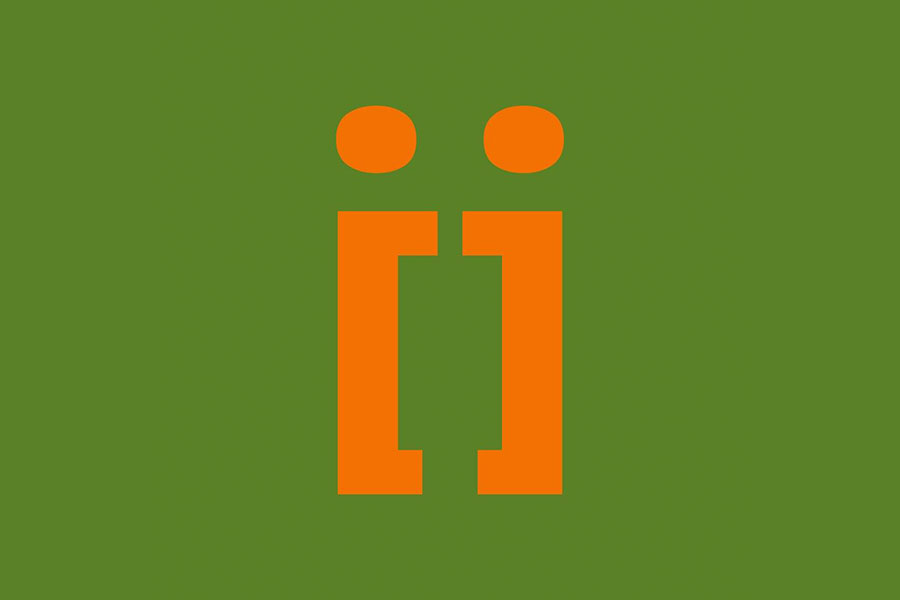
Radar | Sep 24,2022
Abebe Hode, 64, joined the leather industry in the late 1970s, right after graduating from high school.
He first worked for two years in raw leather processing, starting with the removal of hair from the hide or skin. The leather industry at that time was thriving with huge untapped potentials.
Abebe, who now works as quality control supervisor at Colba Tannery, is worried about the industry these days owing to the various challenges he sees. One problem that jumps out at him is the low quality of the raw material that comes in.
“When I started working four decades ago, 80pc of the hide and skin was within grade one to three, and the rejects not meeting export quality were very few,” he said. “Nowadays, the reverse is true as a result of natural or human-caused problems.”
Even though the number of tanneries in the country has grown to 24, the industry’s insiders stress that product quality, lack of access to capital and lack of market integration have created significant roadblocks.
At Colba, where Abebe works, the company has been impacted by these problems leading to production decline. Established in 2009, the tannery produces leather products for shoes, garments, gloves and belts for export to European and Asian countries, and processes up to 6,000 goat and sheep skins and large animal hides daily.
“For the first eight years, we exported up to four containers a month, which is not the case anymore,” said Kebede Amede, a leather technologist at the tannery that employs 300 people.
The company exported products valued at 16 million dollars in 2015. Last year, it saw a dramatic decline that registerd only a third of that figure.
The main cause of the decline in export performance was the directive that made it mandatory to export value-added products.
Tannery drums sit at Colba Tannery in Modjo, where the first processing stage of soaking hides and skins is carried out. The drums can soak up between 3,000 to 4,000 hides and skins at one time.
“The measure is not bad but requires market integration and great financial capacity on the part of the factories to develop the necessary technological capacity to produce competitive finished products and to meet the quality requirements of the importing countries,” argues Kebede.
To succeed in the export of finished leather products, the factory has to be well-equipped with suitable machinery and have a better financial profile, according to professionals working in the industry. They add that this will enable the companies to procure the necessary raw material and cope with the constantly varying needs of clients that follow a frequently changing fashion industry.
Low-quality raw hides and skins collected from local markets are considered one of the major obstacles in the production of quality finished products.
Hides and skins are easily damaged by external parasites that live on the skins of small animals and hides of cattle. Damage also occurs during slaughtering and handling of the raw material prior to its arrival at the tanneries.
“We have stopped engaging in the first stages of raw skin processing because of low-quality raw hides and skins,” said Demberu Yohannes, production head at Friendship Tannery Plc, a Chinese company established almost a decade ago that produces suede, a type of finished leather commonly used for jackets, shoes, shirts, purses and furniture.
“We couldn’t be competitive in the world market with the low-grade hides and skins, so we import wet blue and raw products from Sudan and Saudi Arabia for further processing and manufacturing of our products,” he adds.
The raw materials pass through multiples stages before they come out as finished products. Raw hides and skins are preserved with salt in the first stages and pass through machines and chemicals to be pickled. Then they are processed further and treated with chromium to end up as wet blue hides and skins.
The value of the highest grade of semi-processed hides is three dollars for every square foot and 1.30 dollars for those with lower grades.
Andrea Squillace, 61, an Italian who runs a family-owned leather business from Milan that specialises in gloves and a client of Colba suggests local manufacturers can only gradually become engaged in the production of finished products.
Colba Tannery in Modjo.
“The leather industry doesn’t need too many heavy industries but many small factories that process semi-finished leathers that feed the heavy industry,” says Squillace, who has five decades of experience in the leather industry. “The process of converting semi-finished leather needs a lot of capital and resources.”
The Ethiopian leather industry should have focused on a high-end, high-quality niche market, according to another businessman who has supplied tanneries for over two decades.
He cannot see the prospect of Ethiopian leather companies competing in the semi-finished market against companies in China.
The United Nations Conference on Trade & Development had a similar view as industry professionals in its assessment for the National Green Export Review of Ethiopia last year.
The leather sector is overwhelmed with structural problems ranging from unorganised hide and skin collection systems upstream to poor marketing infrastructure downstream, according to the report.
The report also asserts that Ethiopia has a large comparative advantage in the export of raw hides and skins but not in the export of finished leather products because of a lack of skilled human power and unavailability of needed inputs such as chemicals and high-quality hides and skins.
“The real value addition is still not implemented,” says an expert with vast experience in the leather industry. “The rawhide and skin quality has been declining due to the low attention given by the respective government bodies.”
The expert believes that value addition has not been well executed since there were not support packages given to the factories, when the law that obliged companies to add value was legislated.
The government did not help tanneries create market value chains or aid in sharing the costs of environmental protection and technology, according to the expert.
“Due to these failures, the expectation of the government did not actually materialise,” the expert said.
Ethiopia earned 134 million dollars from leather and leather product exports, according to the Livestock Industry Development Institute, below the targets set by the Second Edition of the Growth & Transformation Plan (GTP II), which is around 280 million dollars.
Raw hides and skins sourced from foreign markets make up 15pc of the market.
Mohammed Aman, assistant professor at Haramaya University’s School of Agricultural Economy & Agribusiness for more than a decade, believes the sector needs an integrated effort between the government and stakeholders.
“The country is losing its known brand of genetic wealth once associated with special breeds that supplied high-quality raw hides and skins to the world tannery market.
The expert recommends that a livestock genetic bank should be established to conserve indigenous cattle. “There must be a win-win strategy that can incentivise the industry as well as ensure that some of the negative impacts such as environmental pollution are addressed.”
Abebe agrees with the view of the expert, especially on the importance of quality cattle breeding. His memories are fresh from the times when strict follow-ups and support for animal husbandry were practiced to protect the hides and skins from parasites and other diseases to sustain quality input.
PUBLISHED ON
Jan 26,2019 [ VOL
19 , NO
978]
Radar | Sep 24,2022
Radar | Feb 06,2021
Fortune News | Dec 28,2019
Fortune News | Jun 14,2020
Radar | Jun 26,2021
Radar | Aug 23,2025
Agenda | Dec 01,2024
Featured | Apr 26,2019
Commentaries | Sep 24,2022
Agenda | Aug 21,2021
Dec 22 , 2024 . By TIZITA SHEWAFERAW
Charged with transforming colossal state-owned enterprises into modern and competitiv...
Aug 18 , 2024 . By AKSAH ITALO
Although predictable Yonas Zerihun's job in the ride-hailing service is not immune to...
Jul 28 , 2024 . By TIZITA SHEWAFERAW
Unhabitual, perhaps too many, Samuel Gebreyohannes, 38, used to occasionally enjoy a couple of beers at breakfast. However, he recently swit...
Jul 13 , 2024 . By AKSAH ITALO
Investors who rely on tractors, trucks, and field vehicles for commuting, transporting commodities, and f...
Aug 23 , 2025
Banks have a new obsession. After decades chasing deposits and, more recently, digita...
Aug 16 , 2025
A decade ago, a case in the United States (US) jolted Wall Street. An ambulance opera...
Aug 9 , 2025
In the 14th Century, the Egyptian scholar Ibn Khaldun drew a neat curve in the sand....
Aug 2 , 2025
At daybreak on Thursday last week, July 31, 2025, hundreds of thousands of Ethiop...