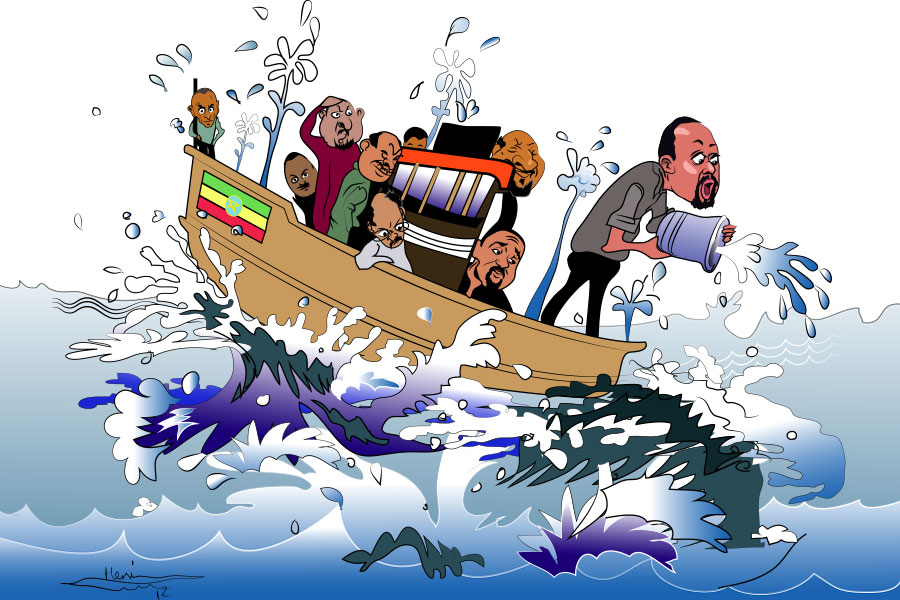
Editorial | May 31,2020
For Walia Tannery, which has been exporting semi-processed hides and skins for close to six decades, the leather business has paid off handsomely to its owners for years.
The company’s annual export tab has reached as high as 12 million dollars, a far cry from Walia’s revenue of one million dollars a year lately.
Located near Drivers & Mechanics Training Centre in Aqaqi Qality District, Walia Tannery has reduced its workforce from 500 to 200 and has seen its manufacturing capacity decrease significantly.
Now, one of the first companies in Ethiopia to be engaged in the export of finished and semi-finished leather products has found itself in a tenuous situation.
“We can’t stand the challenges anymore,” said Yared Alemayehu, general manager of Walia Tannery. “We are about to close our doors.”
Walia’s experience is not singular in the leather industry, as many factories in the country share this narrative.
The industry’s contribution to export revenue has significantly dwindled. In the last fiscal year, the industry generated a mere 130 million dollars in exports, short of the expected 280 million dollars. One-fifth of the export revenue is generated by footwear that is largely exported by one Chinese company.
The industry’s share of the nation’s total export revenue declined to 2.7pc last fiscal year from 3.3pc recorded in the 2012/2013 fiscal year.
According to most observers, the primary culprit for the local tannery industry’s fragile standing is the 150pc taxation that the industry has faced on the export of semi-finished leather products.
The taxation was put into effect by the former Ministry of Finance & Economic Development almost nine years ago to encourage the export of finished leather products.
Since the inception of this government policy a decade ago to essentially halt the export of raw hides and skins and encourage the value-added export of finished leather products, the entire industry has been sliding into a deep decline.
To the fanfare of government officials, the Leather Industries Development Institute (LIDI) and UN agencies, the change in government policy back in 2012 was applauded with the claim that the export of raw hides and skins had deprived Ethiopia of significant benefits.
Batu Tannery built a 25-million-Br secondary water treatment plant in Aqaqi Qality District.
However, the policy has hamstrung the Ethiopian leather industry with the assumption that “Ethiopia has developed the capacity to export finished leather products,” as Solomon Getu, former president of the Ethiopian Leather Industries Association, said at the imposition of the tax.
The emphasis on the export of value-added products, or finished leather and leather products, has led to many tanneries leaving the sector and others like Walia teetering on the brink of collapse.
The special treatment that foreign direct investment receives from the government is another problem pointed out by the local industry.
Local tannery operators complain that the government’s policy favours foreign investors by allowing the importation of second-hand machinery by international companies while prohibiting local tanneries from the same privilege.
The local tanneries are forced to compete globally against well-positioned and well-subsidised foreign manufacturers, who are the recipients of the duty free importation of capital goods, two to eight years of tax holidays, exemption from export taxes, advantageous land-lease arrangements and access to bank loans, while local companies struggle to survive in the business, according to Yared.
“Those local tannery operators should be prioritised and given equal incentives as foreign companies from India and China, who also obtain a 30pc cash subsidy in the name of a modernisation fund,” Yared said.
The quality issue is the other problem. The tanneries are rejecting some 70pc to 80pc of the locally collected rawhide and skins, because it does not meet export quality standards.
Even though the number of tanneries in the country has grown to 26 and employs 6,000 workers, the industry’s insiders stress that this substandard product quality, along with lack of access to capital and market integration has created significant roadblocks in creating a sustainable leather industry in the country.
Hides and skins are damaged by external parasites that live on the skins of small animals and hides of cattle. Poor animal veterinary services, traditional ways of slaughtering and poor collection and handling of hides and skins prior to their arrival at the tanneries are also causing damage.
The quality of the leather is mostly determined at the start of the supply chain with animal husbandry, which has been deteriorating in the country over the last few decades.
Ethiopia has about 57.8 million cattle, 28 million sheep and 28.6 million goats with the potential to collect 3.7 million cattle hides, 8.4 million sheepskins and 7.7 million goatskins annually, according to United Nations Industrial Development Organization (UNIDO).
Besides, the country has lost its once lucrative niche market for a brand of hides derived from distinct genetic sources once associated with special cattle breeds that supplied high-quality raw hides and skins to the world market.
In addition, local leather exporters lost long-developed global clients who received their semi-processed products and tanneries began to scramble for new buyers in a disrupted marketplace caused by the imposition of the 150pc taxation.
Added to the continually deteriorating poor quality of raw material are constant power outages, lack of adequate procurement facilities for imported chemical inputs due to the forex crunch, lack of skilled management, inefficient market development and lack of access to technology that contribute to the industry’s challenges.
Local tanneries also face a major challenge in accessing financing due to collateral requirements, high transaction costs, low credit ceilings set by the banks and high interest rates.
Amid this gloom and doom, Batu Tannery Plc seems to thrive. Batu, which supplies its leather products to global companies as well as local leather product manufacturers like Kangaroo, Anbessa and Jamaica, seems to buck the national trend and has somehow escaped the woes faced by other local operators, according to its general manager, Tatek Yirga.
The company generates five to six million dollars in annual revenue.
It was closed last year for a week, accused of discharging pollutants into the environment. The tannery agreed to build a 25-million Br water treatment plant and brought the factory into compliance with the regulations of the city’s Environmental Protection Authority, which issued the closure order.
Discharges of environmental pollutants from the leather industry need wastewater treatment plants to minimise pollution and the release of toxins into the human and natural environments.
Following an injunction by former Prime Minister Hailemariam Dessalegn in 2017, six tanneries were shut down for a week for violating environmental standards and subsequently built the water treatment plants within the year.
Batu Tannery, Elico Awash, Walia Leather & Leather Products, Dire Industries, Addis Abeba Tannery and New Wing Addis Shoe Factory are companies that were closed until they built waste treatment plants.
Local companies are required to invest in secondary waste treatment plants at a minimum. In Asia, the government subsidises the construction of waste treatment plants as an incentive to the factories and to conserve the environment. The addition of costs associated with such environmental compliance issues are challenges that have led companies like Walia to the brink of collapse.
One of the employees at Walia Tannery, who requested to remain anonymous, has worked for seven years and earnes a monthly salary of 2,100 Br. Supporting a family of five that includes his three kids, he has become restive about the prospect of his continued employment at the factory. He has witnessed the massive reduction of workers in recent years and has taken a part-time job as a security guard.
Some tanneries have also wholly closed their doors. Habesha Tannery, located in Bahir Dar, is one of the foreign companies owned by Turkish nationals that has shut its doors after becoming mired in default proceedings with the Development Bank of Ethiopia.
Habesha commenced operations in 2011 after securing loans from Development Bank and Addis International Bank. When it began operations, it planned to produce crust leather with a target of generating two million dollars a year. However, since last month, the company has entirely ceased operations after defaulting on its loan and has since terminated its 220 workers and closed its doors.
The company has over one million dollars in machinery installed at the factory that is sitting idle, according to Wossen H. Mariam, who was the deputy manager of Habesha.
Habesha is not the only company that went out of business. Over the past couple of years, 10 to 15 tanneries ceased operations, according to data from LIDI, an autonomous body formed to oversee the leather industry.
Industry operators and the policymakers have become somehow disconnected in the last few years, leading the leather industry to suffer and sink into a critical stage, according to Hailekiros Debesay, deputy director general of the Institute.
Recently, the government started giving attention to the industry, making some amendments like removing the 150pc taxation that was imposed on semi-processed leather products. Prime Minister Abiy Ahmed (PhD) has also reshuffled the head position of the Institute at the end of last month.
The taxation of 150pc has since been lifted for ‘crust leather,’ which is dried and tanned leather that has not yet been dyed, but was left intact on all other leather products.
Some industry insiders, including Yared, believe that the taxation has backfired and should be altogether removed from all semi-processed leather products including pickled (a process that makes the hide receptive to tanning) and wet-blue (moist chrome-tanned) leather.
However, an expert with a wide range of experience in the leather industry believes that the companies should focus on exporting value-added products, saying that semi-processed leather does not have the same acceptance in the market like in previous times.
“Due to changes in the fashion industry, the Western desire for finished products has increased,” the expert said.
Teka Gebreyesus, state minister for Trade & Industry, points out that the government is further working to support the local industry through financing and technology and to create efficiencies.
“We will be discussing with the Development Bank how to move forward on this,” Teka told Fortune.
But Yared of Walia seems pessimistic over the industry.
“The only option we currently have is closing the factory,” he laments. “Launching a recovery now doesn’t seem possible.”
PUBLISHED ON
Jun 08,2019 [ VOL
20 , NO
997]
Editorial | May 31,2020
Fortune News | Mar 12,2022
Featured | May 08,2021
Radar | Aug 05,2023
Radar | Apr 27,2025
Fortune News | Dec 30,2023
Fortune News | Sep 06,2020
Fortune News | Aug 28,2021
Featured | Apr 26,2019
Dec 22 , 2024 . By TIZITA SHEWAFERAW
Charged with transforming colossal state-owned enterprises into modern and competitiv...
Aug 18 , 2024 . By AKSAH ITALO
Although predictable Yonas Zerihun's job in the ride-hailing service is not immune to...
Jul 28 , 2024 . By TIZITA SHEWAFERAW
Unhabitual, perhaps too many, Samuel Gebreyohannes, 38, used to occasionally enjoy a couple of beers at breakfast. However, he recently swit...
Jul 13 , 2024 . By AKSAH ITALO
Investors who rely on tractors, trucks, and field vehicles for commuting, transporting commodities, and f...
Jun 28 , 2025
Meseret Damtie, the assertive auditor general, has never been shy about naming names...
Jun 21 , 2025
A well-worn adage says, “Budget is not destiny, but it is direction.” Examining t...
Jun 14 , 2025
Yet again, the Horn of Africa is bracing for trouble. A region already frayed by wars...
Jun 7 , 2025
Few promises shine brighter in Addis Abeba than the pledge of a roof for every family...