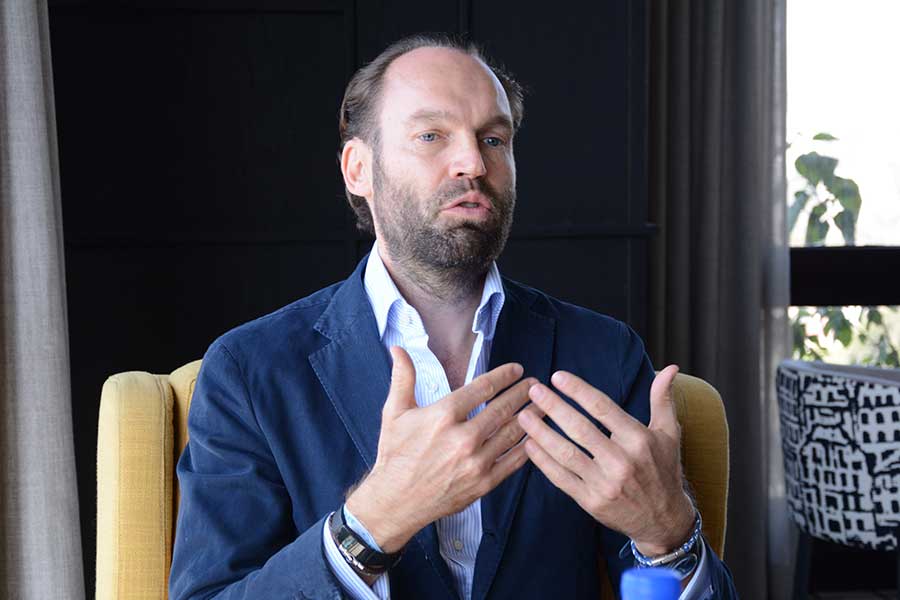
Exclusive Interviews | Dec 12,2020
The factory's floor resembled a beehive, filled with workers rushing to get things done. Two years ago, 126 employees used to work in this plant near Atena Tera, Kolfe Qeraniyo District. Rounding in three shifts, they bottled 5,000lt of water an hour.
Incorporated with 600,000 Br in initial capital in 2016, the medium-sized Al-Aki Trading Plc bottles Ambassador Water.
Then the COVID-19 pandemic hit. As economies worldwide went into lockdown, demand for consumer goods plummeted. Factories everywhere cut down productivity while workers were laid off. Everyone at Al-Aki Trading was on their toes, but none anticipated that the worst was yet to come.
The post-lockdown jump in demand, combined with a global shipping crisis, caused the prices of raw materials to skyrocket. The rise in petroleum prices over the past year has exacerbated the situation for Al-Aki, which requires large amounts of polyethylene terephthalate (PET) for its bottles. It is a powder moulded into plastic bottles and containers to package foods, beverages, and consumer products. Like most raw materials used to produce plastics, PET is a derivative of oil and natural gas, directly tied to international market prices.
The company had to cut production down to 1,500lt an hour.
Over the past year, Al-Aki's factory floor has lost its characteristic scene, with some employees put on paid leave while revenues plummeted. Both of its production lines were almost at a standstill last week. Machines were running below capacity, and there were not many hands around to load what little raw materials were available. There was only one managerial staff member was in the office.
It was Tamiru Gadisa, a tall and dark-skinned man. He was coordinating the activities of two workers near the water filling system.
For most of the last five years, Tamiru, 35, put in eight-hour workdays as a supervisor, earning a gross salary of 6,700 Br. A father of two, he supports his family in a studio apartment in Burayu, on the outskirts of Addis Abeba, paying 3,000 Br for rent.
Tamiru saw the workforce at Al-Aki's reduced by a third over the past two years. It makes him anxious that his own future is not secured.
"If the factory is shut, where would we go?" he wondered.
Alone in the bottled water testing room sat Asmamaw Addis, 25. The microbiologist seemed a little melancholy. The lab he works in is one of two the plant operates, including a facility that analyses the chemical content in the water the plant bottles. Both are small, each no larger than four square meters of space partitioned with glass walls. They are flooded with white fluorescent lights, beaming on the shelves stocked with various reagents and chemicals on one side. Asmamaw and other technicians were clad in white gowns, with hoods to cover their heads. But facilities lack the odour that reminds casual visitors of typical laboratories.
"We're not doing as much as we used to," Asmamaw told Fortune.
The shortage of raw materials is a serious concern for the management. Abdulsemed Kedir serves as the general manager of Al-Aki Trading. He constantly worries about the prospect for his workers if the plant is closed.
"Where do we put them?" he puzzled. "The situation is too stifling."
Abdulsemed is not alone in his moment of despair. Nearly all in the manufacturing sector that depend on raw materials imported from abroad are in the same boat of frustration. Around 2,610 firms operate in eight broad industries, from food and beverages and textiles and apparel to chemical products and plastic products. How dependent they are on imported raw materials may differ, with those in the textiles, leather, tobacco, and furniture accounting for 50pc. The chemical, plastic and engineering industries depend heavily on imported inputs, some of them spending 99pc of total costs on imported raw materials.
The unavailability of raw materials due to severe forex shortage limits manufacturers across industries to 26pc of installed capacity, finds a report from the Ministry of Trade & Regional Integration. The most productive utilise 45pc of capacity.
Among the hardest hit are plastic manufacturers, operating under 35pc. Close to 450 medium- and large-scale manufacturers produce 12 categories of goods, including automotive tires, plastic home partitions, PVC tiles, and household furniture. They had an aggregate output of 400,000tn in five years. These manufacturers employ close to 11,000 workers.
Polymers are the most widely used raw material in Ethiopia, accounting for more volume than steel, copper, and aluminium combined. Various methods – extrusion, injection moulding, blow moulding, and roto moulding – are used to process them into finished products.
Mintu Plast Plastic Raw Material Production Plc is one of the importers of polymers and polyvinyl chloride (PVC) worth 10 million dollars each year from China, Korea, and India. It supplies pre-form containers to companies like Al-Aki Trading. However, it stopped importing polymers last year due to the surge in prices in the international market.
“This is in addition to the foreign currency shortage we're facing,” said Genene Lemma, general manager of Mintu Plast, incorporated in 2003 with 13 million Br in equity.
Companies like Al-Aki Trading are entirely dependent on imports for raw materials for plastic production. In the four years beginning 2016, the country imported 1.9 million tonnes of plastics in polymers and primary forms worth 3.1 billion dollars, according to the data obtained from the Chemical & Construction Inputs Industry Development Institute.
Plastics in primary forms account for 65pc of the total. The average import bill for plastic raw materials ranges between 500 million and 750 million dollars a year. The country imports 75,000tn of PET, an essential component of plastic bottles used by bottlers such as Al-Aki, worth 105 million dollars annually. High-density polyethylene (HDPE), the other raw material popular in Ethiopia, is used to produce containers, shopping bags, water pipes and jerrycans. Close to 80,000tn of HDEP, worth 110 million dollars a year, was imported, a value half the PVC import bills. The 40,000tn shipped each year are used to make cosmetics containers, plumbing pipes and fittings, and electrical conduits.
This makes Ethiopia the second-largest importer of plastics in primary forms in east and central Africa, according to the Association for Plastics & Rubber Machinery Manufacturers of Europe.
However, South Korea, Thailand, and China are the primary sources of plastic raw materials shipped to Ethiopia, although the raw materials are produced mainly in oil-rich Middle Eastern countries such as Saudi Arabia and the United Arab Emirates (UAE).
Tana Plastic Factory Plc is one of the oldest industries in Ethiopia. It was established over 50 years ago and produced materials made of plastics such as pipes, conduits, plastic cups and garden hoses. In the Arada District behind Holy Trinity Cathedral School, the factory has been unable to use more than a third of its production capacity since last September. Its managers say the plant has almost been idle this year.
To the managers' sigh of breath, the raw materials they had ordered recently arrived at Djibouti ports. They hope the shipment on the way will keep the plant operating for the next four months, according to Wolde Assena, major shareholder and former general manager of Tana Plastic.
Tana Plastic opened a letter of credit (LC) with Zemen Bank for 120,000 dollars. Its managers were contemplating opening LCs with other commercial banks before they ran short of inputs again.
“We've not been lucky so far," said Wolde.
Troubled by such challenges, the Ethiopian Plastic & Rubber Manufacturers Association urged the National Bank of Ethiopia (NBE) authorities to allocate foreign currency to save the industry from total collapse. A survey conducted by the industry lobby group, established in 2004, reveals 80pc of the 400 manufacturers under its wing produce at less than half their capacity.
“The government has been responding to our demands,” said Mentesinot Lemma, president of the Association. “We're hoping the response will be the same this time around.”
His sanguinity is grounded on a policy decision authorities in the Ministry of Finance took in July last year, eliminating the five percent customs tax imposed on PVC imports. The Association plans to request custom duties be lowered on di-sec-octyl phthalate, the most widely used general-purpose plasticiser for the manufacturing of flexible plastics; and chlorinated paraffin wax, another plasticiser used in the manufacturing of PVC compounds for wires and cables.
Mentesinot argues that the impact of taking such measures goes beyond plastic industries.
“Many depend on the materials supplied by plastic factories,” he said.
These include the packaging and construction industries. Polypropylene and polyethylene are vital inputs for the food packaging industry, while PVC is used for construction materials like window frames. There are also industrial linkages between packaging manufacturers and agro-processors. Yet, the effects are perhaps most readily visible in water bottling companies.
Factory-gate prices for a pack of two-litre bottles have nearly doubled to 90 Br over the past few months. Consumers are left to shoulder the burden, paying 20 Br for a single two-litre bottle at kiosks. The price was 13 Br in the not-too-distant past.
In April last year, bottlers lodged complaints and a plea for assistance before the authorities, claiming that issues with foreign currency shortages and disruptions in the supply of raw materials have placed them in dire straits. The industry's misgivings were submitted through the Ethiopian Bottled Water, Soft Drink, Fruits & Vegetable Processing Industries Association. Leaders of the Association, which comprises 83 members, have also filed their complaints with the Customs Commission, claiming taxation imposed on importing raw materials is "unfair".
Bottlers like Al-Aki Trading have been sourcing raw materials from local retailers for more than 200pc in recent months. The price for a 40gm two-litre pre-form jumped dramatically from 2.8 Br to 8.8 Br in one year.
But blaming the forex crunch for the plastic industry's woes is only part of the picture, according to Yonas Abate, director of plastic and rubber industries at the Chemical & Construction Inputs Industry Development Institute. Other factors contribute to the shortage of raw materials.
“The jump observed in oil prices has pushed the prices of plastic raw materials drastically," he said.
The militarised conflict in Ukraine has further pushed international market prices for oil; it shot up by nearly a third to 123 dollars in the weeks following Russia's aggression.
Zelealem Berhanu, an independent consultant who has been advising Ethiopian Plastic & Rubber Manufacturers Association, says discouraging the use of "unnecessary" materials like plastics bags can be one way to cope with the challenges. Neighbouring Kenya has banned the use of plastic bags, outlawing it as environmentally damaging. Ethiopia has yet to follow suit.
However, the per capita use of plastics in Ethiopia has increased by about 15pc annually over the last decade – from 0.6Kg in 2007 to 3.2Kg in 2020. It is much lower than the global average of 28Kg in per capita use of plastics.
“Reducing the production volumes of some important petrochemical products through enhanced recycling is another alternative,” said Zelealem.
Both rigid and flexible plastics are used in Ethiopia, ensuring a sufficient feedstock supply for the recycling process. Zelealem recommends substituting the fossil fuel-based feedstock with biomass-based alternatives to lower local manufacturers' dependence on imported raw materials.
The agriculture sector has the potential to produce enough biomass, he argues. Studies show that Ethiopia can produce up to 1.7 million tonnes of biomass annually.
The consultant also recommends banks stop providing LCs to plastic importers, instead allocating the foreign currency to the manufacturers.
The federal government is exploring the viability of plastic raw materials from natural gas derivatives as a substitute. However, the outcome and recommendations from such surveys might arrive too late for people like Tamiru from Al-Aki to save their livelihood. He is already on edge about the prospect of losing his job.
Sixteen of his colleagues recently left because the company could not raise their pay.
PUBLISHED ON
Apr 02,2022 [ VOL
23 , NO
1144]
Exclusive Interviews | Dec 12,2020
Exclusive Interviews | Oct 09,2021
Fortune News | Jul 06,2025
In-Picture | Nov 16,2019
My Opinion | Feb 12,2022
Fortune News | Dec 11,2021
Radar | Sep 26,2021
Fortune News | Oct 23,2021
My Opinion | May 23,2021
Photo Gallery | Oct 06,2021
Dec 22 , 2024 . By TIZITA SHEWAFERAW
Charged with transforming colossal state-owned enterprises into modern and competitiv...
Aug 18 , 2024 . By AKSAH ITALO
Although predictable Yonas Zerihun's job in the ride-hailing service is not immune to...
Jul 28 , 2024 . By TIZITA SHEWAFERAW
Unhabitual, perhaps too many, Samuel Gebreyohannes, 38, used to occasionally enjoy a couple of beers at breakfast. However, he recently swit...
Jul 13 , 2024 . By AKSAH ITALO
Investors who rely on tractors, trucks, and field vehicles for commuting, transporting commodities, and f...
Aug 23 , 2025
Banks have a new obsession. After decades chasing deposits and, more recently, digita...
Aug 16 , 2025
A decade ago, a case in the United States (US) jolted Wall Street. An ambulance opera...
Aug 9 , 2025
In the 14th Century, the Egyptian scholar Ibn Khaldun drew a neat curve in the sand....
Aug 2 , 2025
At daybreak on Thursday last week, July 31, 2025, hundreds of thousands of Ethiop...