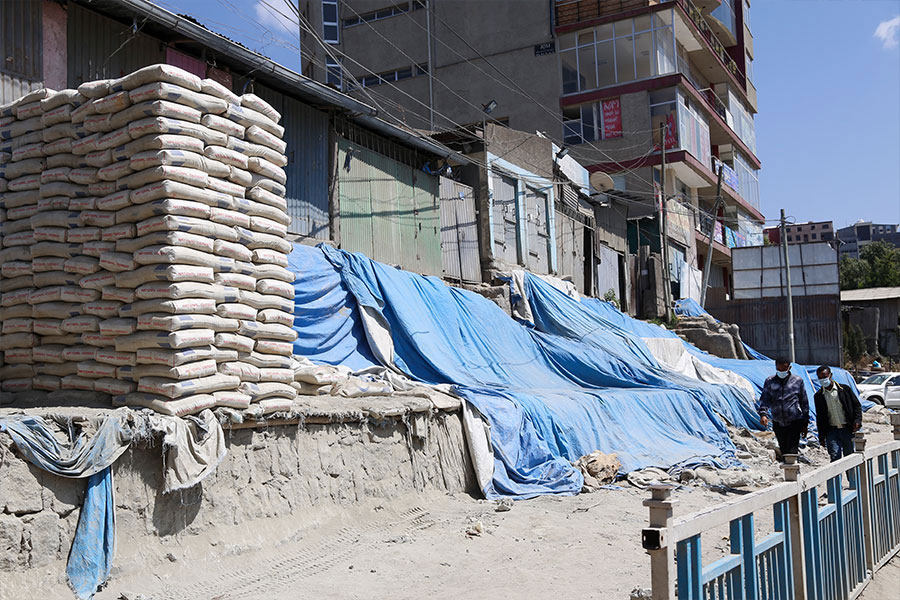
Fortune News | Jun 25,2022
The federal government looks to pin its hopes on a novel construction material to tame the ballooning input prices choking the construction industry.
Officials are preparing standards for interlocking and compress-stabilised blocks – bricks that can slot together easily without mortar. Interlocking concrete blocks are an ideal option for an industry where cost and time are crucial. Standards are necessary for uniform quality, the facilitation of production, the commercialisation and use of the blocks on a larger scale, says Tewodros Tegegne, head of the Construction Industry Reform Office under the Ministry of Urban Development & Infrastructure.
Gedlu Mulugeta is the owner of the invention. A year ago, he received a patent for his interlocking blocks from the Ethiopian Intellectual Property Office. Over the past decade, he has been managing a company, Gedlu Mulugeta General Contractor, and experimenting with interlocking blocks for the past four years.
“After receiving a patent certificate, I decided to apply for standards to pave the way for large-scale production,” he told Fortune.
A technical committee comprising members from the Ministry, the Ethiopian Standards Agency, and Addis Abeba University evaluated the proposal before embarking on the preparation of standards. Incorporated 10 years ago with 1.2 million Br capital, Gedlu's construction company produces and supplies 4,000 hollow concrete blocks a day. The absence of standards limits large-scale production of interlocking blocks, despite growing demand, according to Gedlu.
He said that the blocks are easy to install and require few materials and specialist labour.
“The assessment showed that the blocks have huge potential to reduce the cost of construction,” said Tewodros.
The Ministry forwarded the proposal to the Agency three months ago. The Standards Agency has thus far prepared over 10,000 voluntary and mandatory national standards, with a little less than 2,000 of these applying to construction materials such as cement, metal sheet roofing, and nails. The preparation of standards can take up to six months, Solomon Wubshet, team leader of civil engineering and construction standards at the Agency, toldFortune.
“The standards will be finalised by the end of the budget year,” said Solomon.
The development may provide some breathing room to contractors, who have been in an uproar over the skyrocketing prices for building materials seen over the past few years. Combined with the COVID-19 pandemic and the foreign currency crunch, jacked-up prices have pummeled the construction industry, contributing to nearly a fifth of the country's gross domestic product (GDP).
Industry players are desperate to cut costs on inputs such as cement, which is crucial to make the mortar that holds together the bricks and concrete blocks most commonly used in Ethiopia. Cement – or its unavailability – has been haunting contractors over the past couple of years. Prices have also tripled to over 700 Br a quintal. Despite authorities' efforts to tame the surging prices and improve supply, including setting price caps, the situation has not improved.
Another basic component used by the construction industry is hollow concrete blocks, one of Ethiopia's most extensively used walling materials. The blocks are near-ubiquitous and can be used for load-bearing walls and non-load-bearing walls. However, there are no standards for the production of hollow concrete blocks.
According to Solomon, the Agency is preparing standards for regular concrete blocks and the hollow, solid, and stabilised varieties as well.
Globally, mortarless brick construction is gaining momentum for it reduces construction time and costs. Although different types of concrete blocks, such as hollow and u-shaped, have been introduced to Ethiopia in recent years to build low-cost housing projects, the culture of using interlocking, mortarless blocks remains rare.
Gedlu and three researchers from Bahir Dar University, who created compress-stabilised blocks, hope this will change soon. Compress-stabilised blocks are made from dry, inorganic subsoil, non-expansive clay, aggregates and Portland cement. A study conducted at the University reveals that compress-stabilised blocks are half as expensive as concrete blocks, according to Rahel Ayalew, construction technology and management lecturer at Bahir Dar University.
The drop in prices comes mainly from the low volume of cement required to produce compress-stabilised blocks.
PUBLISHED ON
Apr 30,2022 [ VOL
23 , NO
1148]
Fortune News | Jun 25,2022
Agenda | Sep 28,2024
Fortune News | Mar 19,2022
Radar | Aug 25,2024
Agenda | Oct 17,2021
Commentaries | May 28,2022
Radar | Jul 20,2019
In-Picture | Jun 30,2024
Fortune News | May 02,2020
Life Matters | Nov 09,2024
Dec 22 , 2024 . By TIZITA SHEWAFERAW
Charged with transforming colossal state-owned enterprises into modern and competitiv...
Aug 18 , 2024 . By AKSAH ITALO
Although predictable Yonas Zerihun's job in the ride-hailing service is not immune to...
Jul 28 , 2024 . By TIZITA SHEWAFERAW
Unhabitual, perhaps too many, Samuel Gebreyohannes, 38, used to occasionally enjoy a couple of beers at breakfast. However, he recently swit...
Jul 13 , 2024 . By AKSAH ITALO
Investors who rely on tractors, trucks, and field vehicles for commuting, transporting commodities, and f...
Jul 5 , 2025
Six years ago, Ethiopia was the darling of international liberal commentators. A year...
Jun 28 , 2025
Meseret Damtie, the assertive auditor general, has never been shy about naming names...
Jun 21 , 2025
A well-worn adage says, “Budget is not destiny, but it is direction.” Examining t...
Jun 14 , 2025
Yet again, the Horn of Africa is bracing for trouble. A region already frayed by wars...