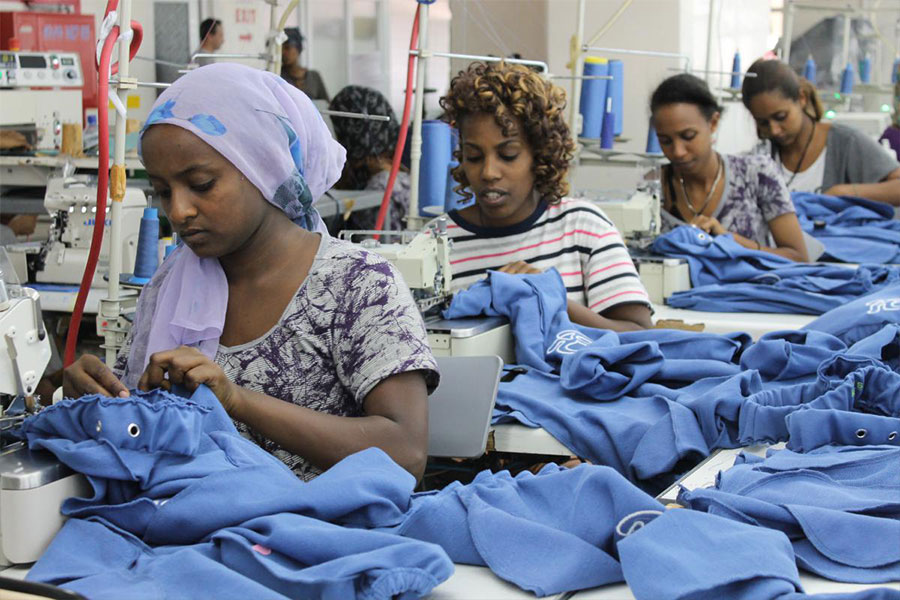
Fortune News | Jul 23,2022
The Leather Industry Development Institute has begun supplying locally-made machinery to small and medium-scale leather and leather product manufacturers. Previously, nearly all domestic companies were buying their machinery overseas.
As of last month, the Institute has started supplying four types of machinery for shoemakers, and it is in the process of availing one piece of machinery for belt makers. Heat reactivator; embossing; portable sloe; and brushing and polishing units are the specific machines made available for sale to the shoemaking factories. The reactivator is utilised to fasten the sole to the leather, while the embossing machine is used for logo stamps. The sloe machine is used to adjust the edges and shapes of shoes.
Enterprises in the business were facing challenges in acquiring these machines, and because of this many of them have been using outdated equipment in their operations, according to Fitsum Abate, an expert at the Institute's Technology Transfer & Training Directorate.
So far, 41 leather factories have shown interest in purchasing the machinery from the Institute, which conducted assessments of the leather industry to identify the problems of the sector. Conducted two months ago on companies located in Addis Abeba and Oromia, and Southern Nations, Nationalities & People's regional states, the input assessment revealed that factories are facing problems mainly due to a lack of machinery.
The assessment finding revealed that leather product factories had shown interest in buying 33 heat reactivator, 31 embossing, 10 brushing and polishing, and 23 portable sloe machines.
"We aim at increasing productivity in the leather industry," said Berhanu Serjabo, director of communication affairs at the Institute.
The leather companies have been buying the machines from abroad, investing anywhere between half a million to a million Birr for a single machine.
The cost will be reduced by half or more when factories buy the machines from the Institute, according to Fitsum. The locally-made machines at the Institute are sold for between 300,000 Br to 600,000 Br.
Anbessa Shoe SC, a local leather products manufacturer, is among the companies that has shown interest in buying the machinery from the Institute. The company used to import all its machinery from abroad.
This loses the firm lots of money as it purchases the equipment at higher costs, according to Yigermal Melkamu, administration manager at Anbessa.
"It'll help us in reducing the cost of production," Yigermal told Fortune.
The Engineering Service Directorate within the Institute is manufacturing the machinery. So far, eight machines have been made. The team sources the spare parts from the local market and uses imported machines as prototypes for the design and manufacture of their versions.
The Directorate is also planning to hire additional engineers to produce the machines en masse, according to Maru Hailu, an electrician at the engineering service workshop.
Capital goods are the most needed factor of production in such sectors where there are local raw materials available, according to Tekie Alemu (PhD), an assistant professor of economics at Addis Abeba University. He appreciated the initiative of local production but urged constant mass production.
"With the limited foreign currency and minimal financial capabilities of factories," he said, "importing these machines is very difficult."
Many countries, such as Japan and China, have efficiently copied and manufactured machinery originally made in the West, argued Tekie.
"The government should also direct technical schools to take such initiatives to copy and manufacture machinery that is currently being imported," said the expert. "The country should imitate not only simple tools but also sophisticated machinery."
Tekie said that there is a specialisation problem within the leather industry, which has 84 leather and leather product makers, and it keeps the cost of production high for enterprises. He recommended that the Institute also help the sector in terms of value chain development and in establishing linkage between producers.
Albeit the target, the revenues generated from the export of leather and leather products stood at 80.1 million dollars in the last fiscal year. The government expects this figure to grow to 100 million dollars this year from the export of 66 million square feet of leather, 2.3 million pairs of shoes, 1.3 million leather gloves, and 516,000 leather garments.
PUBLISHED ON
Nov 14,2020 [ VOL
21 , NO
1072]
Fortune News | Jul 23,2022
Radar | Oct 12,2024
Radar | May 21,2022
Fortune News | Apr 22,2022
View From Arada | Aug 03,2025
Dec 22 , 2024 . By TIZITA SHEWAFERAW
Charged with transforming colossal state-owned enterprises into modern and competitiv...
Aug 18 , 2024 . By AKSAH ITALO
Although predictable Yonas Zerihun's job in the ride-hailing service is not immune to...
Jul 28 , 2024 . By TIZITA SHEWAFERAW
Unhabitual, perhaps too many, Samuel Gebreyohannes, 38, used to occasionally enjoy a couple of beers at breakfast. However, he recently swit...
Jul 13 , 2024 . By AKSAH ITALO
Investors who rely on tractors, trucks, and field vehicles for commuting, transporting commodities, and f...
Aug 23 , 2025
Banks have a new obsession. After decades chasing deposits and, more recently, digita...
Aug 16 , 2025
A decade ago, a case in the United States (US) jolted Wall Street. An ambulance opera...
Aug 9 , 2025
In the 14th Century, the Egyptian scholar Ibn Khaldun drew a neat curve in the sand....
Aug 2 , 2025
At daybreak on Thursday last week, July 31, 2025, hundreds of thousands of Ethiop...