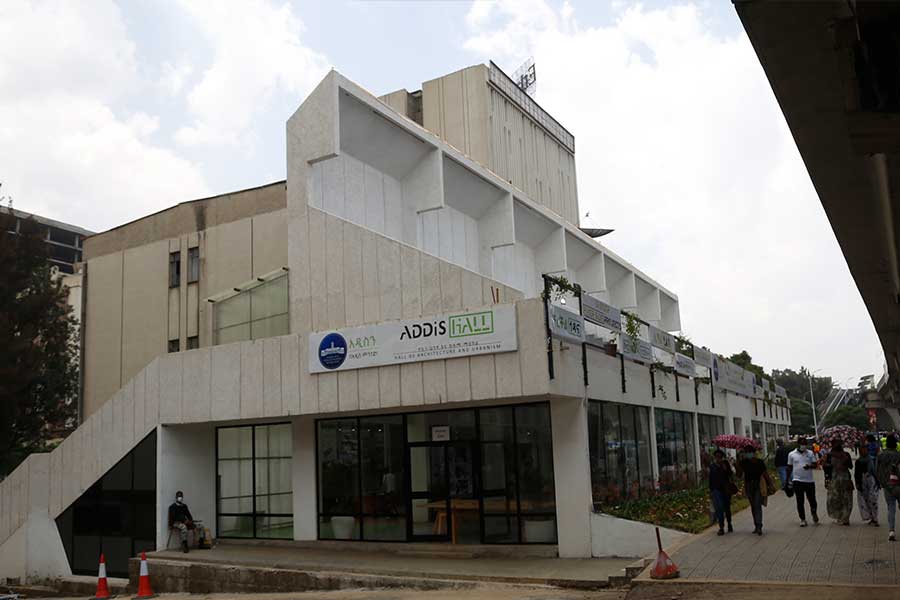
Fortune News | Jul 13,2020
With the main aim of mitigating crop loss, the Ethiopian Biotechnology Institute has invented a multi-crop thresher with financial support from USAID.
The thresher has the capacity to thresh 1,000tn of crops a day, and it can be operated by just two people.
The machine's research, design and training budget consumed close to 70,000 dollars. It threshes corn, wheat, barley and teff. USAID's programme Feed the Future Ethiopia Value Chain Activity covered 60,000 dollars of the cost for the machine. The remaining cost was covered by the Institute.
The process starts at the top of the machine by hand feeding the crops into the threshing chamber. Once it enters, a rotating drum beats the grain off the stalks. Chaff from the threshed grain falls through a sieve-like structure called a concave. A fan blows dust and small chaff from the threshed grain, which then leaves the machine through an exit chute to be collected in bags.
The thresher is also equipped with two wheels, an indented seat and a hitch, so that it can easily be pulled by a vehicle or a person.
The Institute and USAID also trained six researchers and 20 manufacturers on the design and production of the machinery in November. The training was given by collaborating with Soyabean Innovation Lab from America, three Ghanaian trainers and Wolkite Polytechnic College.
The thrasher aims to improve quality of life, strengthen value chains, and contribute to food security, according to Eyobel Gebresenbet, director of reverse engineering at the Institute.
"It will also save the crop from unseasonal rain and create job opportunities for the manufacturers and youths from rural areas who migrate to urban areas," he told Fortune.
However, it is too expensive to buy the engine, according to him.
In the beginning, the Institute faced challenges in getting the engine; however, as an alternative it started using a tractor engine from the Adama Engineering factory for the three prototypes. The prototypes were produced by trainees of Wolqite Polytechnic College within one week.
Before inventing the machinery, the Institute, which is tasked with identifying problems in agriculture, the manufacturing industry and environmental engineering, conducted research that took eight months.
Wolkite Polytechnic College was selected for the project because of its human resources, machinery and convenient workshops, according to Bogale Tekle, vice-dean of Wolqite Polytechnic College.
‘‘It produces cleaner agricultural products," he said. "It also reduces the amount of hard labour and drudgery."
Agriculture contributes around 34pc to gross domestic product (GDP) and employs two-thirds of the adult population. Seventy-two percent of the agriculture sector is comprised of crop production.
Over 10,000 square kilometres of land was used to grow cereal crops last harvest season, a third of which was utilised for teff, the nation’s staple grain.
The total production in last year's Meher season, the main growing season that starts in May and ends in September, was about 50.2 million quintals.
Even though Ethiopia is known to be an agrarian community, productivity is very low due to crop loss and lack of agricultural mechanisation.
During the harvest season, 25 to 30pc of the produced crops are wasted, according to data from the Ministry of Agriculture.
Since the machine would be expensive, farmers should consider organising themselves to buy the machine, according to Daniel Dentamo, communications team leader at the Ministry of Agriculture.
‘‘If the farmers can buy the machine easily, it will save energy and time,’’ said Daniel.
Habtamu Tsegaye, a crop chain value advisor at USAID's Feed Future Ethiopia programme, says that the private sector should take the lead in distributing these machines to the farmers.
‘‘It is very difficult for the manufacturers to both produce the machine and distribute it to the farmer,’’ said Habtamu.
Habtamu says that the government should support and work to link the manufacturer and farmer in order to make the process transparent.
No matter how late the technology is, it reduces labour and pollution from unwanted crops, and it increases the quality of agricultural products and the economy, according to Fentahun Tesfa, assistant professor at Bahir Dar University’s College of Agriculture & Environmental Sciences.
‘‘It saves energy that is wasted during post-harvest,’’ said Fentahun. "So far, the existing technology has been slow to save the harvested agricultural product.’’
But Fentahun opines that farmers might take time to get used to such a new product.
‘‘Thus, the government and agricultural associations should aggressively promote it,’’ he said.
The Institute plans to pilot the machine in Zeway, according to Eyobel.
PUBLISHED ON
Jan 11,2020 [ VOL
20 , NO
1028]
Fortune News | Jul 13,2020
Fortune News | Jun 29,2019
Fortune News | Jan 12,2019
Fortune News | Aug 29,2020
Radar | Apr 20,2019
Fortune News | Apr 22,2022
Radar | Jun 27,2020
Fortune News | Apr 15,2023
Radar | Apr 20,2019
Radar |
Dec 22 , 2024 . By TIZITA SHEWAFERAW
Charged with transforming colossal state-owned enterprises into modern and competitiv...
Aug 18 , 2024 . By AKSAH ITALO
Although predictable Yonas Zerihun's job in the ride-hailing service is not immune to...
Jul 28 , 2024 . By TIZITA SHEWAFERAW
Unhabitual, perhaps too many, Samuel Gebreyohannes, 38, used to occasionally enjoy a couple of beers at breakfast. However, he recently swit...
Jul 13 , 2024 . By AKSAH ITALO
Investors who rely on tractors, trucks, and field vehicles for commuting, transporting commodities, and f...
Aug 30 , 2025
For Germans, Otto von Bismarck is first remembered as the architect of a unified nati...
Aug 23 , 2025
Banks have a new obsession. After decades chasing deposits and, more recently, digita...
Aug 16 , 2025
A decade ago, a case in the United States (US) jolted Wall Street. An ambulance opera...
Aug 9 , 2025
In the 14th Century, the Egyptian scholar Ibn Khaldun drew a neat curve in the sand....