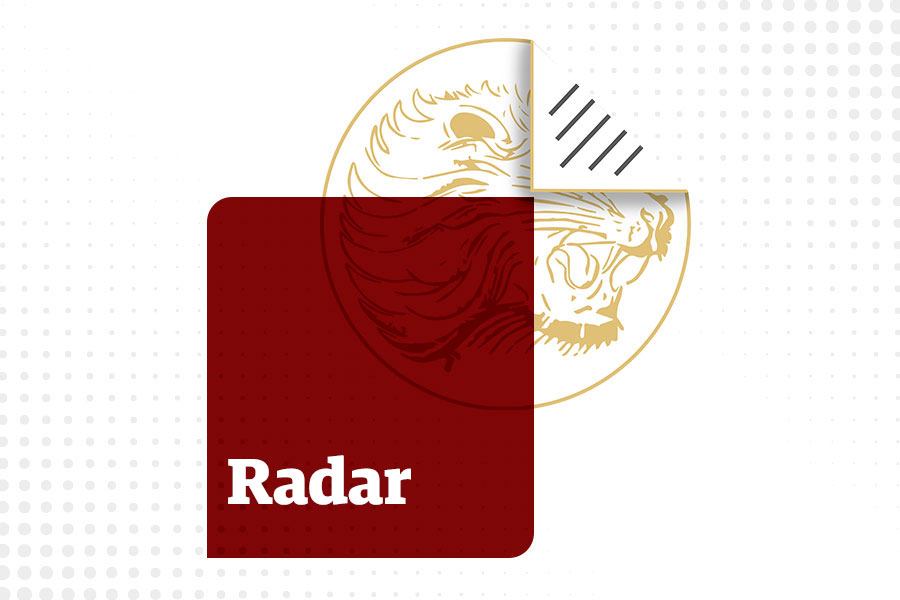
Radar | Nov 30,2019
A bottleneck in the national supply chain risked the cement market emptying stores and retailers last week. Shops in the Megenagna area, a hub for cement retail in Addis Abeba, were closed due to the scarce supply.
“Only two retailers’ were open in Megenagna,” a salesperson who requested anonymity said.
Those opened were selling gypsum.
According to the retailers, the shortage has been an issue for over three months. Stores were sitting idle while overhead costs caught up with them. The shops are rented for up to 40,000 Br in monthly rent in the area.
“We don’t know how long we can keep our doors open,” another store owner told Fortune.
Retailers take up to 1,000 quintals of cement a day on regular days. Prices soared to 1,800 Br for a quintal in the retail market, with distributors such as the Ethiopian Industrial Input Development Enterprise and the Ethiopian Trading Businesses Corporation supplying retailers with 1,300 Br. The distributors buy directly from factories for 770 Br and 870 Br.
“People have become idle and lost their jobs because of supply shortage,” said Zekarias Tsegaye, a truck driver who delivers cement for buyers. “It’s become challenging for me to support my family.”
Trade officials told retailers three months ago to be patient. Still, retailers had no supply last week from an industry with over 14 cement plants having an aggregate production of 8.4 million tonnes annually. Demand is estimated to have reached 12 million tonnes.
A few of the largest factories have ceased production, attributing their decision to security issues where their plants are located. For over a week, Derba Cement has stopped production. The Nigerian Dangote has also stopped supplying cement to the market following sharp disagreements with trade authorities who cap wholesale prices at factory gates.
Three months ago, authorities at the Ministry of Trade & Regional Integration (MoTRE) reintroduced price caps, compelling cement factories to sell a quintal of cement to designated distributors, increasing the value by close to 67pc. The authorities' attempt to regulate the supply chain faced a backlash and pushed retail prices to an unprecedented 1,500 Br a quintal.
Retailers blame intermediaries for playing a significant role in the dramatic rise of cement prices. Earlier this year, the Ministry’s officials attributed the shortages to the intermediaries, pledging that there is no shortage of the product.
However, the Enterprise tasked by federal authorities to distribute cement says it has not received a supply for a week.
“Intermediaries have cement in their hands, not distributors,” Solomon Geresha, Deputy Chief Executive Officer, told Fortune.
Dangote Cement has been providing the Enterprise with 11 trucks of cement a day, amounting to 4,400 quintals. Solomon and his team urged the company to raise the deliveries to 20 trucks. National and Derba cement factories have stopped supplying the Enterprise.
Derba Cement, 70km northwest of the capital, remains the most prominent plant producing 2.5 million tonnes, followed by Dangote’s 2.3 million tonnes annual production.
Haile Assegid, general manager of Derba Cements, told Fortune the factory is not producing cement due to security concerns in the area.
“It’s also under maintenance,” he said.
The CEO of National Cement, Fitsum Demisse, declined to comment.
Despite the misgivings in the retail market for the unavailability of cement for sale, the factories’ unresolved issue with the Ministry, and ongoing security concerns, federal authorities insisted there is no problem with production and supply.
Kumneger Ewnetu, the Trade Ministry’s communications director, echoed the sentiment last week, speaking with Fortune.
Flintstone Engineering Plc is a construction which undertook more than 80 projects since its incorporation in 1991.
The company gets cement for selected projects contracted from the government, including five public projects. Contractors like Flintstone receive cement directly from factories after the Trade Ministry permits them.
“It’s not enough, though,” said Biruk Shimelis, deputy general manager, whose company has been supplied by Mugher.
The company ceased construction on 20 of its real estate projects. However, cement is not the only challenge in the industry. Biruk urged federal authorities not to get involved in the market as it only exacerbates the situation.
Cement delivery takes over three months after acquiring permits from the Ministry and paying in advance. A contractor in the industry for over a decade, working on an irrigation project in Bale, Oromia Regional State, paid in advance for 1,000 quintals of cement to Mugher Cement three months ago. It has yet to be delivered late last week.
PUBLISHED ON
Oct 22,2022 [ VOL
23 , NO
1173]
Radar | Nov 30,2019
Radar | Jun 24,2023
Radar | Jul 23,2022
Radar | Mar 09,2019
Fortune News | Aug 22,2020
Radar | May 20,2023
Radar | Oct 12,2024
News Analysis | Apr 22,2023
Radar | Mar 23,2019
Fortune News | Dec 29,2018
Dec 22 , 2024 . By TIZITA SHEWAFERAW
Charged with transforming colossal state-owned enterprises into modern and competitiv...
Aug 18 , 2024 . By AKSAH ITALO
Although predictable Yonas Zerihun's job in the ride-hailing service is not immune to...
Jul 28 , 2024 . By TIZITA SHEWAFERAW
Unhabitual, perhaps too many, Samuel Gebreyohannes, 38, used to occasionally enjoy a couple of beers at breakfast. However, he recently swit...
Jul 13 , 2024 . By AKSAH ITALO
Investors who rely on tractors, trucks, and field vehicles for commuting, transporting commodities, and f...
Aug 23 , 2025
Banks have a new obsession. After decades chasing deposits and, more recently, digita...
Aug 16 , 2025
A decade ago, a case in the United States (US) jolted Wall Street. An ambulance opera...
Aug 9 , 2025
In the 14th Century, the Egyptian scholar Ibn Khaldun drew a neat curve in the sand....
Aug 2 , 2025
At daybreak on Thursday last week, July 31, 2025, hundreds of thousands of Ethiop...